Unprecedented Supply Chain Visibility
SIMBA Chain has a proven track record of delivering secure, verified data exchange management solutions for multiple government departments and agencies. Most recently, SIMBA has deployed a Digital Thread solution within the Department of Defense (DoD). The solution, built for the United States Air Force (USAF), tracks over 2000 parts across hundreds of suppliers and delivers a single, authoritative source of truth for the stakeholders within the USAF.
This is the first time the USAF has achieved a 360º view of their supply chain – improving military readiness, business intelligence, and operations. The solution is customizable, and lives on top of existing data networks, meaning there is no need to retire legacy systems or adopt a new architecture.
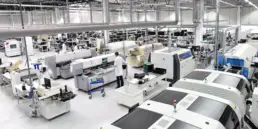
Solution Overview:Built for DoD
- Built for the U.S. Air Force
- Focused on critical air defense platforms to strengthen supply chain readiness
- Tracked thousands of parts from hundreds of suppliers
- USAF has increased visibility and reduced resources required to attain and analyze data
How SIMBA’s Digital Thread Solution Works
The integration of data from ERP, MES, and PLM systems provides comprehensive visibility into production details, including specific tasks performed and the time taken to complete them. This capability enables organizations to monitor ERP orders down to sub-tier suppliers, offering a complete overview of the entire manufacturing process. This level of unprecedented detail is revolutionary and provides an authoritative source of truth.
SIMBA Empowers the Digital Thread with:
- An authoritative source of truth (ASOT).
- Seamless, secure data sharing across teams, departments, and even external partners.
- Integrity of your data that preventing any unauthorized alterations or tampering.
- Robust provenance tracking, providing a clear, auditable record of your data’s origin and history.
- Streamlined workflows, reduced costs, and accelerated innovation.
- Faster data-driven decisions and optimized supply chains.
- A way to bring cutting-edge products to market quicker.
Commercial Digital Thread Initiatives
Aerospace & Defense
Lockheed Martin: Uses digital thread technology to enhance the design and production of the F-35 fighter jet. The company integrates data from design, manufacturing, and operational phases to ensure the aircraft meets stringent performance and safety standards.
GE Aerospace: Implements digital threads to connect data from aircraft engine design, manufacturing, and maintenance. This integration helps improve engine performance, predict maintenance needs, and reduce downtime.
Automotive
BMW: Employs digital threads to link data from vehicle design, production, and customer usage. This integration supports better design iterations, more efficient manufacturing processes, and improved customer experiences.
Ford: Uses a digital thread to connect its design, engineering, and manufacturing processes. This connectivity allows for real- time data sharing and collaboration, leading to reduced development cycles and enhanced product quality.
Manufacturing
Siemens: Utilizes digital thread technology in its manufacturing operations to connect design data with production and operational information. This integration helps optimize manufacturing processes, improve product quality, and support predictive maintenance.
GE: Applies digital threads across its various business units to connect data from product design, manufacturing, and operation. For example, in its wind turbine division, GE uses digital threads to monitor turbine performance and predict maintenance needs.
Electronics
Medtronic: Employs digital threads to connect data from the design, manufacturing, and post-market surveillance of its medical devices. This integration ensures compliance with regulatory requirements and improves the safety and effectiveness of its products.
Johnson & Johnson: Utilizes digital thread technology to link data from the development, manufacturing, and distribution of its medical devices. This connectivity helps J&J enhance product quality, ensure regulatory compliance, and improve patient outcomes.
Medical Devices
Apple: Implements a digital thread approach to integrate data from product design, manufacturing, and customer feedback. This connectivity helps Apple streamline its supply chain, improve product quality, and enhance customer satisfaction.
Samsung: Uses digital threads to connect data from the design and manufacturing of its electronic devices. This integration helps Samsung optimize its production processes, reduce defects, and accelerate product development cycles.
Talk to Us
Learn more about Digital Thread or how to implement secure verifiable data exchange across your networks and systems.